Custom Spring Manufacture
A Spring For Every Requirement
Need a hard-to-find spring replicated, or are you looking for a custom solution? We have the answer, from industrial and manufacturing applications to apparatus that demands ultra-fine tolerances. Every spring is produced to your exact specification using Computer controlled (CNC) technology. If you want to buy compression springs, tension or torsion springs, contact National Springs & Wire Products.
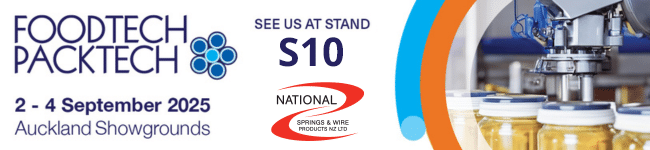
“It’s never enough to just manufacture products for customers. We find ways to innovate and provide solutions through client and employee feedback. Having this culture in a business, where opportunity to expand knowledge and understanding with the help of the experts; translating technical information to a more user-friendly language, makes a significant effort to provide customers with a positive experience. That is how we make a difference.”
Ethel Tabobo
Internal Office Support
Wire diameter range
Stainless Steel
0.20mm and above
Pre-galvanized
0.63mm and above
Hard Bright
0.315mm and above
Mild Steel
0.315mm and above
Frequently Asked Questions
What materials are used for making springs?
The most common carbon steel spring material used in New Zealand is Hard Drawn AS1472 Range 2, this is supplied phosphate or galvanised coated. The most common Stainless steel comes in JIS G4314 304 or 316.
What coating options are available?
Springs can be zinc, nickel or other plating’s using electrolysis, they can also be powder coated or painted.
What are important considerations in spring design?
Spring design involves various considerations to ensure the spring functions effectively and meets the desired requirements. Here are some important considerations in spring design:
Load Requirements:
- Understand the specific load or force requirements the spring needs to handle. Consider both static and dynamic loads, assembled and working lengths
Material Selection:
- Choose an appropriate material based on factors like tensile strength, yield strength, fatigue resistance, and corrosion resistance.
Helix and Pitch:
- Determine the number of coils, helix angle, and pitch to achieve the desired spring rate and load-carrying capacity.
Wire Diameter:
- Select an appropriate wire diameter considering the material properties, space constraints, and the required strength.
Coil Diameter and Spring Length:
- Determine the coil diameter and overall length of the spring to meet the spatial constraints of the application.
Ends and Hooks:
- Choose the type of ends or hooks based on the application requirements. Common types include closed and open ends, as well as various hook configurations.
Stress Levels:
- Ensure that the stresses in the spring, such as shear stress, bending stress, and torsional stress, are within acceptable limits to avoid premature failure.
Fatigue Life:
- Consider the number of cycles the spring is expected to undergo and design for an appropriate fatigue life. This involves evaluating stress levels and material fatigue properties.
Service Environment:
- Account for the environmental conditions the spring will be exposed to, including temperature, humidity, and the presence of corrosive substances.
Frequency of Operation:
- Take into account the frequency and amplitude of the spring’s oscillations, as this can impact fatigue life and performance.
How do you make a spring softer? Less force
To make a spring softer and reduce its force, you generally have a few options:
Decrease Wire Diameter:
- Reducing the wire diameter of a spring reduces its stiffness, which means that the spring requires less force to achieve a given amount of deflection or compression.
Increase the Coil Diameter:
- Increasing the coil diameter of a spring can make it softer because it alters the geometry of the spring, leading to a reduction in the spring constant or stiffness, this will also increase the deflection/compression.
Increase the Number of Coils:
- Increasing the number of coils in the spring can make it softer. This is because adding more coils increases the overall length of the spring and the number of turns, which can result in a lower spring rate. This will also increase the deflection/compression.
Use a Softer Material:
- Choosing a material with a lower modulus of elasticity or a lower tensile strength can make the spring softer. However, changing the material may also affect other properties, so it’s crucial to consider the overall impact on performance.
Alter End Configurations:
- Changing the end configurations of the spring, such as using a different type of end or modifying the hooks, can influence the spring’s behaviour. However, this might have a more subtle effect compared to adjusting wire diameter or coil count.
Heat Treatment:
- Subjecting the spring to a heat treatment process, such as annealing, can help relax the material and reduce its stiffness. Be cautious with this method, as excessive heat treatment may affect other material properties.
How do you make a spring stronger? More force
To make a spring stronger, meaning that it can exert more force for a given amount of deformation or compression, you can consider the following design modifications:
Increase Wire Diameter:
- A larger wire diameter increases the strength of the spring. This is because the cross-sectional area of the material is directly related to its strength. Increasing the wire diameter increases the amount of material resisting deformation, thus making the spring stronger.
Reduce Coil Diameter:
- Decreasing the coil diameter increases the spring constant and, consequently, the force exerted for a given displacement. This is particularly effective when combined with an increase in wire diameter.
Decrease Number of Coils:
- Removing coils from the spring decreases the number of active coils, which can enhance the overall strength. However, this may also make the spring stiffer, so it’s important to strike a balance between strength and flexibility.
Use a Higher Strength Material:
- Selecting a material with a higher tensile strength can significantly increase the strength of the spring. Keep in mind that other material properties, such as ductility and fatigue resistance, should also be considered.
Heat Treatment:
- Heat treatment processes, such as hardening or tempering, can increase the strength of the spring material. These processes alter the internal structure of the material to enhance its mechanical properties.
Optimize Spring Geometry:
- Adjusting the design parameters, such as the pitch, end configurations, or overall length, can influence the strength of the spring. Careful optimization can help achieve the desired strength while maintaining other performance characteristics.